The manufacturing industry is undergoing a radical transformation thanks to automation equipment. From increasing efficiency to reducing operational costs, automation has revolutionized how businesses create products and compete in a global market. With emerging technologies and innovative tools taking centre stage, manufacturers can now automate complex processes, enhance quality, and achieve unprecedented precision.
This comprehensive guide dives into the world of automation equipment, exploring how it is shaping modern manufacturing while equipping businesses with the tools they need to succeed in an ever-evolving industry.
What is Automation Equipment?
Automation equipment refers to the machinery, tools, and technologies designed to perform tasks with minimal human intervention. These systems integrate software, robotics, sensors, and AI to execute repetitive or intricate operations efficiently and consistently. In manufacturing, automation equipment includes assembly lines, robotic arms, CNC machines, conveyor belts, and advanced control systems.
The use of automation equipment is no longer limited to large-scale factories; even small and medium enterprises (SMEs) are leveraging these tools to streamline processes, improve accuracy, and cut costs.
The Role of Automation in Modern Manufacturing
Automation plays a pivotal role in driving innovation and productivity. By automating mundane and labour-intensive tasks, manufacturers can focus their workforce on value-added activities like product design and process improvement. Additionally, automation fosters scalability, allowing businesses to adapt quickly to fluctuations in demand.
Key benefits of automation equipment include:
- Improved Efficiency: Automated systems run continuously without breaks, significantly boosting productivity.
- Enhanced Precision: Machines execute tasks with consistent accuracy, reducing errors and waste.
- Cost Reduction: Automation minimizes labor costs and operational inefficiencies.
- Increased Safety: By handling dangerous tasks, automation equipment ensures a safer work environment.
Essential Types of Automation Equipment in Manufacturing
Industrial Robots
Industrial robots are versatile and can perform tasks such as welding, painting, and material handling. These robots are programmed to work with speed and precision, making them essential for repetitive tasks that require a high degree of accuracy.
Programmable Logic Controllers (PLCs)
PLCs are computer-based control systems used to automate machinery and processes. They monitor inputs and outputs, ensuring smooth operations by following pre-set instructions.
CNC Machines
Computer Numerical Control (CNC) machines are vital for cutting, drilling, and shaping materials with exceptional precision. They are widely used in industries like aerospace, automotive, and electronics.
Conveyor Systems
Conveyor systems are used to transport materials and products between different stages of production. These systems ensure seamless workflow and reduce manual handling.
Sensors and Actuators
Sensors collect real-time data, while actuators convert this data into physical actions, such as adjusting machine speed or temperature. Together, they form the backbone of modern automation systems.
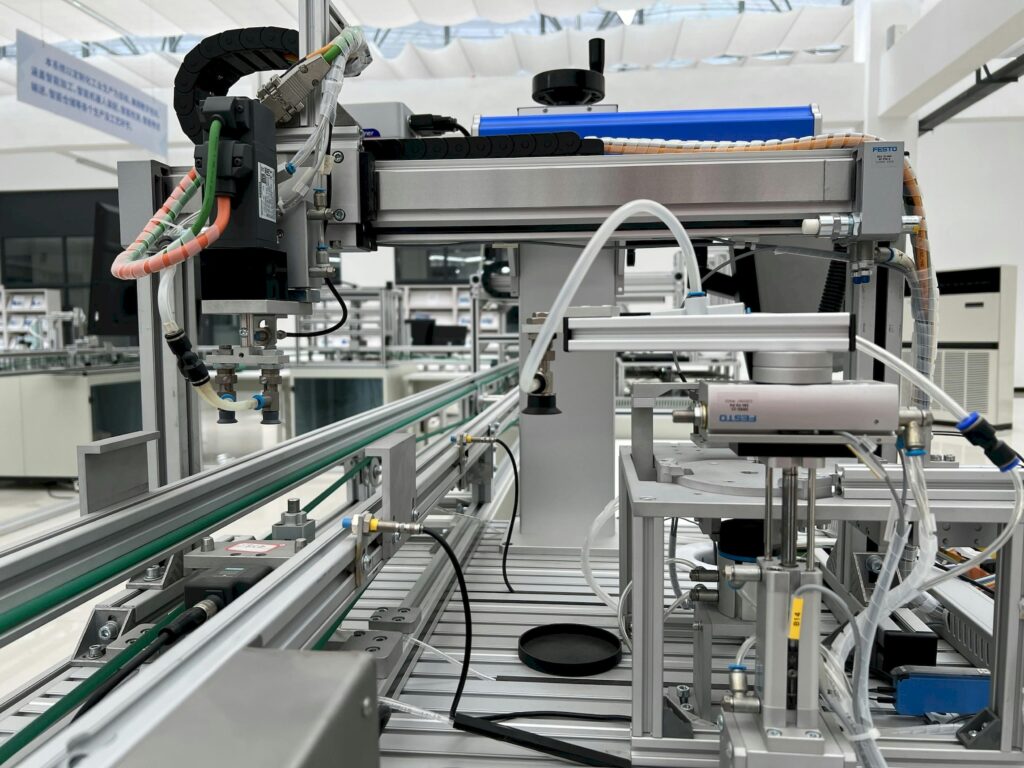
The Impact of Automation Equipment on Quality Control
One of the most significant advantages of automation is its impact on quality control. Automated systems ensure consistent production standards by eliminating human errors. For instance, machine vision systems can inspect products for defects with unparalleled precision, ensuring only high-quality items reach the market.
Real-time monitoring and feedback loops further enhance quality by enabling instant adjustments to processes. This proactive approach minimizes downtime and prevents costly mistakes.
How Automation Equipment Drives Cost Efficiency
Automation equipment transforms cost structures in manufacturing by reducing waste and optimizing resource utilization. For example, robotic arms can handle materials more efficiently, minimizing spillage or damage. Additionally, predictive maintenance systems use AI to forecast equipment failures, enabling timely repairs and preventing expensive breakdowns.
Overcoming Challenges in Automation Adoption
While automation offers numerous benefits, its implementation comes with challenges. High initial investment costs, employee resistance, and the need for specialized skills are common hurdles. However, these challenges can be addressed through strategic planning, employee training, and government incentives.
Manufacturers must also ensure cybersecurity to protect their automated systems from potential threats. Investing in robust security measures and staying updated on the latest technologies can mitigate risks effectively.
How to Choose the Right Automation Equipment
Selecting the right automation equipment depends on various factors, including:
- Industry Requirements: Determine the specific tasks that need automation.
- Budget: Evaluate the upfront costs and long-term savings.
- Scalability: Choose equipment that can adapt to future needs.
- Vendor Support: Ensure the supplier provides training and maintenance services.
- Integration Capabilities: Opt for systems that can seamlessly integrate with existing processes.
FAQs
What is the difference between industrial robots and collaborative robots?
How does automation equipment improve efficiency?
What industries benefit the most from automation?
Is automation equipment affordable for small businesses?
What role does AI play in automation equipment?
How does automation contribute to sustainability?
Conclusion
Automation is no longer a luxury but a necessity in modern manufacturing. By embracing these technologies, businesses can enhance productivity, improve quality, and achieve cost efficiency while staying competitive in a dynamic market. As innovation continues to shape the future of automation, manufacturers must adapt and invest in the right tools to stay ahead of the curve.